Last updated on
Understanding various types of dredge equipment is vital because it can enhance efficiency in executing excavation activities aimed at gathering bottom sediments and disposing them at a different location.
From the construction of new maritime pathways to the maintenance of existing waterways, dredging stands as a critical process in shaping our aquatic infrastructure. Spanning across various environments and challenges, the technology behind this mighty task has evolved to meet every specific need.
As you delve into the world of dredge equipment, understanding the nuanced capabilities of mechanical and hydraulic machines—from the meticulous precision of cutter suction dredgers to the robust agility of backhoe dredgers—is essential.
Whether you’re dealing with a congested harbor, a silted channel, or a bed of rocky substrate, this article guides you through the wide array of dredging equipment that ensures efficient sediment relocation and waterway maintenance.
Prepare to discover how each type of dredger aligns with your project’s goals, optimizing the balance between environmental considerations and industrial demands.
Key takeaways:
- Mechanical dredgers: bucket ladder, grab, backhoe (flexible for various sediments)
- Hydraulic dredgers: cutter suction, plain suction, trailing suction hopper (efficient in sediment loosening and long-distance pumping)
- Cutter suction dredgers: precise excavation for ports, harbors, channels
- Grab or clamshell dredgers: targeted dredging and debris removal
- Backhoe dredgers: effective for confined spaces and rocky substrates
Mechanical Dredgers
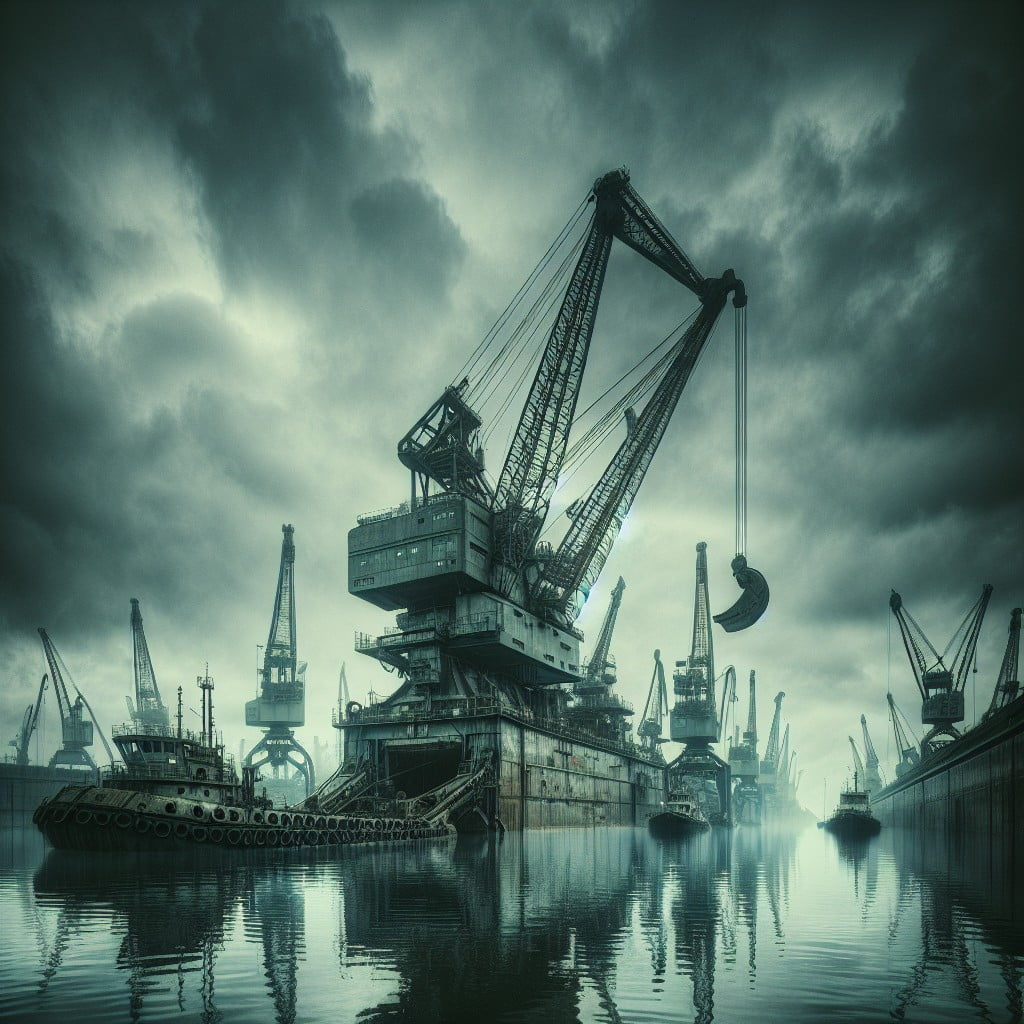
Mechanical dredgers operate much like an excavator’s arm, equipped with a device to remove sediment from the bottom, transfer it, and at times, load it for disposal. Their operation is quite straightforward:
- Bucket Ladder Dredgers have a series of buckets mounted on a wheel or ladder, scooping material as the wheel turns, an operation similar to a giant chain of buckets working on a continuous loop.
- Grab or Clamshell Dredgers utilize a crane with a grab or clamshell bucket to pinch and pick up substrate from the waterbed. This method is precise, ideal for targeted dredging and handling debris-laden material.
- Backhoe Dredgers resemble standard backhoes but are on a floating platform. They are suitable for rocky substrates, with a strong digging force and the ability to handle large boulders.
This range of equipment offers flexibility in handling various sediments, suitable for harbor maintenance, canal deepening, or coastal protection projects. Each has its unique strengths, whether it’s the precision of a grab dredger or the robust bucket ladder’s efficacy in continuous operations.
Bucket Ladder Dredgers
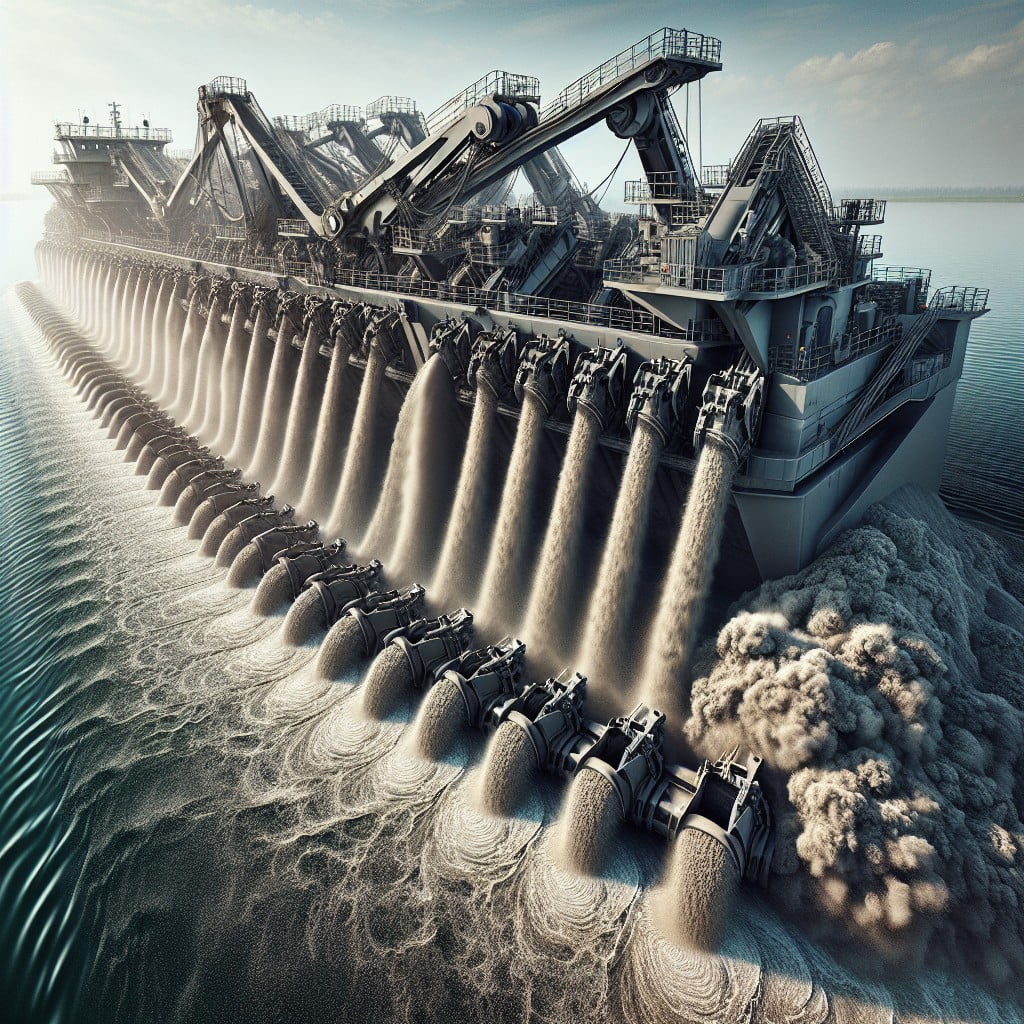
These vessels feature a series of buckets attached to a circular ladder, offering continuous excavation. As the buckets rotate, they scoop material from the seabed, elevating it and discharging it onto a chute leading to barges or a designated disposal site.
Key Characteristics:
- Effective in hard-packed soils or materials thanks to their robust digging capability.
- Their design allows for precise control, making them suitable for targeted dredging around structures such as piers.
- Often seen in calm waters, such as canals and harbors, where their methodical operation is most efficient.
- Less suitable for areas with environmental sensitivity due to the potential for increased turbidity.
Applications:
- Ideal for mineral mining operations underwater, including tin, gold, and other valuable materials.
- Employed in maintenance dredging where a high level of accuracy is required.
- Flood defense projects and restoration of aquatic habitats also benefit from their precision.
Their operational mode demands careful coordination, utilizing a series of winches and spuds to stabilize the dredger while the bucket ladder excavates and moves along the dredge site.
Grab or Clamshell Dredgers
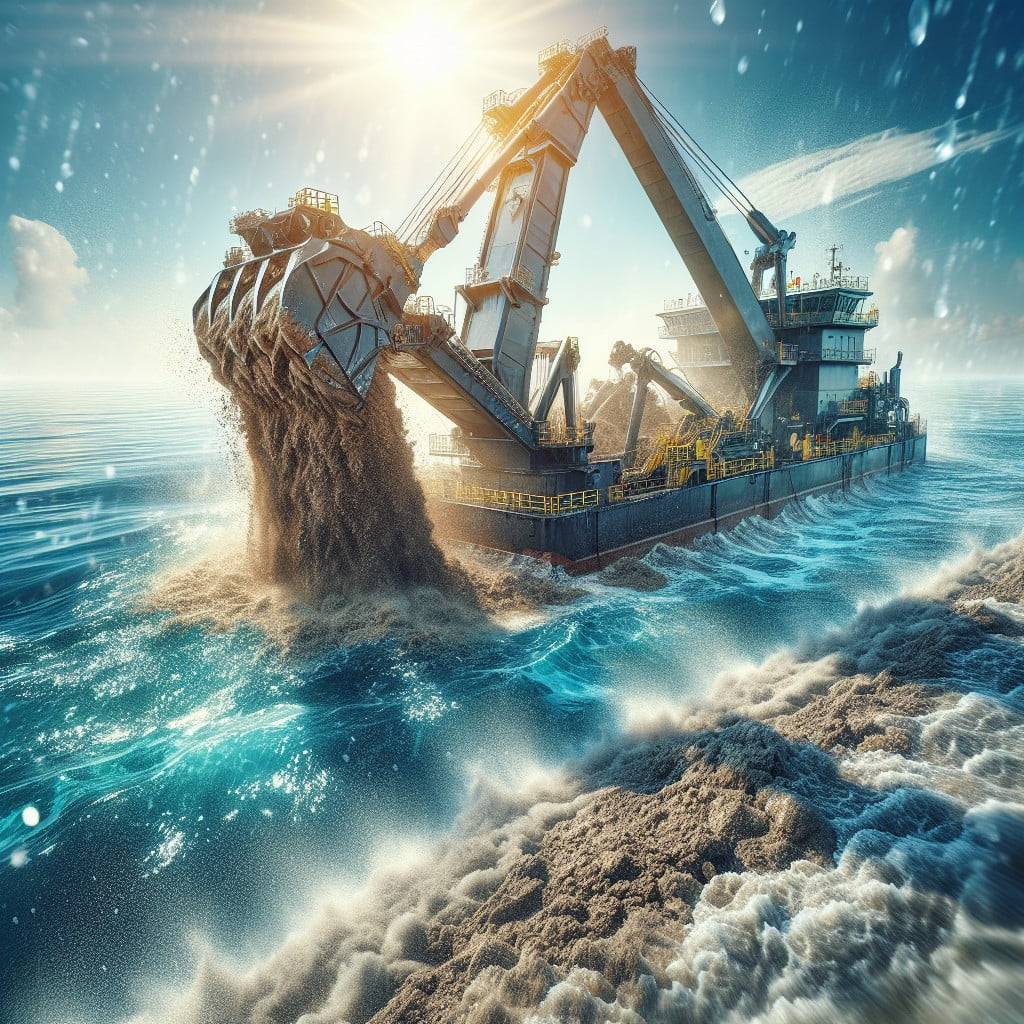
Favored for their precision in excavation, grab dredgers operate by deploying a hinged shell bucket that opens to scoop up material and then closes to retain it. These machines are particularly efficient in removing debris from specific areas, such as the corners of docks or around pylons.
Their operation is relatively straightforward: the dual scoops descend into the water, guided by a crane on a barge or a spud, directly targeting the sediment or debris. Once filled, the bucket is hoisted and emptied into a separate barge or disposal area.
Key points:
- Ideal for targeted dredging and debris removal from specific spots.
- Stationary position during operation; requires repositioning to cover different areas.
- Flexibility in dealing with a variety of materials, including heavy and compacted soils.
- Typically used in enclosed spaces like harbors due to their precise maneuvering capabilities.
- Less efficient for bulk clearing compared to other dredge types.
Grab dredgers are particularly useful in small-scale projects and areas that are difficult to reach, providing a surgical tool in the dredger’s arsenal.
Backhoe Dredgers
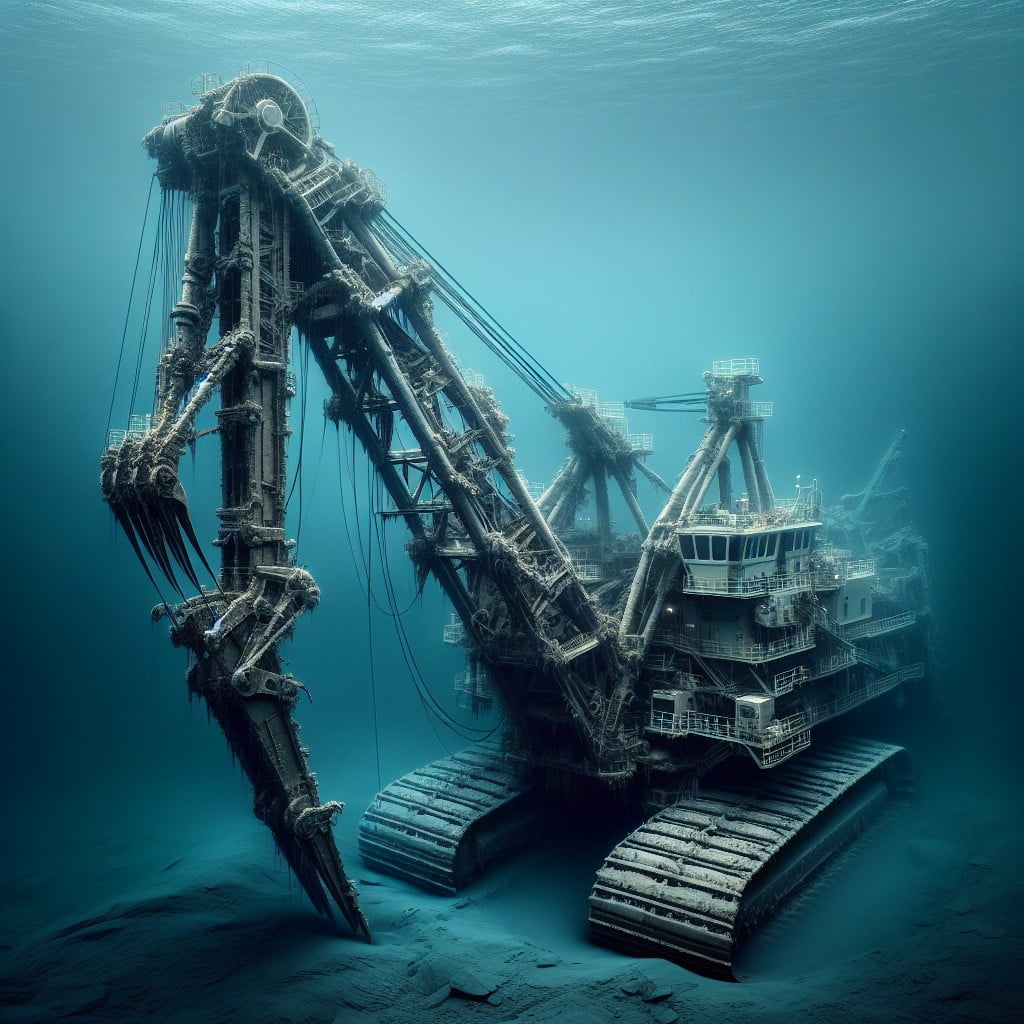
Equipped with a powerful hydraulic arm and a bucket, these dredgers excavate material much like land-based backhoes. The arm is capable of reaching significant depths and is especially effective in digging precise trenches for pipelines or cables.
The dredged material is scooped into the bucket and then lifted to be deposited onto adjacent barges or onto the shore for disposal. Ideal for small to medium-scale projects, they’re particularly adept at working in confined spaces, such as harbors and alongside piers.
Their operation depends on the skill of the operator to handle the digging and maneuvering, which can affect the efficiency and precision of the dredging process.
Hydraulic Dredgers
Hydraulic dredgers operate by sucking a mixture of water and sediment from the seabed, much like a giant vacuum cleaner. The core types include:
Cutter Suction Dredgers (CSD): These employ a rotating cutter head to dislodge sediment, which is then sucked up by a powerful centrifugal pump. They are well-suited for heavy sediment and can create precise cuts, making them ideal for channeling, harbor construction, and land reclamation.
Plain Suction Dredgers: These omit the cutter head and are used for softer materials like silt or fine sand. They are effective in situations where precision is less critical, such as maintaining depths in harbors or navigation channels.
Trailing Suction Hopper Dredgers (TSHD): These self-propelled vessels incorporate suction pipes and a hopper to collect the dredged material. The hopper allows them to transport and dispose of the materials at sea or to a designated location, which is particularly useful for projects situated at a substantial distance from the disposal area.
Hydraulic dredgers are generally more efficient in terms of sediment loosening and collection when compared to mechanical dredgers. Their effectiveness in long-distance pumping also helps in reducing the need for secondary transport, hence optimizing operational costs. However, they require clear water to function efficiently and can be constrained by the presence of large debris or rocks.
Cutter Suction Dredgers
Cutter suction dredgers (CSDs) are a versatile choice for many dredging operations, featuring a revolving cutter head to break up hard soil or rock. They work by cutting and fragmenting material, which is then sucked up through a pipeline system. The spoil is removed through a floating pipeline and can be deposited a considerable distance from the site, often onto land, into a barge, or deposited back into the aquatic environment in a controlled manner for land reclamation purposes.
Notably efficient in creating precise depths, these dredgers are commonly used for port, harbor, and channel dredging due to their accuracy. The stationary positioning of CSDs during operation allows for meticulous work in preparing foundations for maritime structures, like quays and jetties.
Equipped with a powerful engine, they are suitable for challenging terrains, including rock, clay, and coral. The cutter head’s design can vary depending on the specific requirements of the project—different teeth and armoring can be fitted to optimize performance according to the material being dredged.
With their combination of robustness and precision, CSDs are an indispensable piece of equipment for projects requiring meticulous excavation or where the sediment proves too resilient for less heavy-duty machinery.
Plain Suction Dredgers
Designed to handle fine materials, these dredgers are equipped with a centrifugal pump to create a vacuum, effectively elevating loose sediments such as silt, sand, and gravel. They lack the cutting mechanism found in other hydraulic dredgers, thus are not suitable for compacted soil. The working principle relies on suction alone, akin to a giant vacuum cleaner for underwater sediments.
The versatility of these dredgers allows for a broad spectrum of applications, including maintaining depths of waterways and harbors where the sedimentation of particles occurs regularly. Additionally, they are beneficial for sand mining, where the extracted sand is often used in construction.
The simplicity of their design means fewer moving parts, contributing to lower operational costs and maintenance. This simplicity, however, also limits their application to environments where material can be easily sucked, without the need for prior loosening.
Trailing Suction Hopper Dredgers
Trailing suction hopper dredgers (TSHDs) are self-propelled vessels that operate on a different principle than stationary dredgers. Equipped with suction pipes, often one on each side, these pipes trail over the dredge site as the vessel moves. The drag heads collect material by sucking it like a giant vacuum cleaner from the seabed.
An onboard hopper serves as a storage compartment for the dredged material, allowing these dredgers to transport sediments over long distances. The size of the hopper determines the capacity and, as a result, the efficiency of the operations. Once full, the hopper can be closed, and the TSHD transports the collected materials to the designated disposal or processing location.
A noteworthy feature is the dredge’s ability to work in various environments – from harbors and channels to more open and deeper waters. The versatility of TSHDs makes them perfect for projects where navigation is essential, and least disturbance to commercial operations is desired.
Their design also allows for continuous operations, which is particularly beneficial for large-scale projects. However, precision work may be limited due to the moving nature of the vessel, making them less suitable for detailed excavation tasks.
For projects that require dredging and offsite disposal of material without disrupting marine traffic, TSHDs offer a flexible, robust, and effective solution.
Choosing the Right Dredger for the Project
Identifying the optimal dredger for a particular project hinges on several key factors that must be carefully evaluated to ensure efficiency and cost-effectiveness. Material type is of primary concern; cohesive sediments like clay necessitate a cutter suction dredger for its precision and power, while loose materials such as sand might be easily managed by a trailing suction hopper dredger.
The project’s scale also influences the choice. Large-scale, ongoing projects often benefit from the high-capacity output of trailing suction hopper dredgers, which can operate independently and navigate longer distances with the dredged material. Conversely, smaller, localized projects may be more suited to a backhoe dredger, which offers simplicity and maneuverability in confined spaces.
Depth and accessibility of the project site must not be overlooked, as deeper excavations require equipment such as deep suction dredgers with extended capabilities. Similarly, restricted sites with limited access might necessitate more compact and versatile machinery.
Ultimately, selecting equipment is a balance between the nature of the project, the physical environment, and economic considerations. Matching the dredger to these parameters promotes operational success, ensuring a streamlined process from start to finish.
Considerations Based On Material Type
Selecting the appropriate dredging equipment hinges on the characteristics of the material to be excavated. Dense materials such as gravel, clay, and compacted sand necessitate powerful cutting tools found in cutter suction dredgers. These devices can break down the material before suctioning it out.
For loosely packed sediments like silt or fine sand, a plain suction dredger proves efficient, capitalizing on the ease of material removal without the need for cutting apparatus. Coarser material with large debris, commonly found in harbor dredging, often requires the robust, pinching action of a grab dredger to manage the irregular load sizes.
Tailoring equipment choice to the material ensures maximized productivity and minimizes wear on machinery, leading to a smoother dredging process and longer equipment lifespan. Understanding the material also guides the decision-making process about subsequent handling, transport, and disposal methods, integrating the dredging operation into a seamless flow.
Considerations Based On Project Scale
Project scale is a critical factor in selecting the appropriate dredging equipment. Large-scale projects often require heavy-duty machines such as cutter suction dredgers or trailing suction hopper dredgers, known for their efficiency in extensive operations, such as creating new harbors or waterways.
For small to medium projects, such as canal maintenance or environmental remediation, smaller hydraulic dredgers or mechanical dredgers like backhoes may be more suitable. These machines offer the precision needed for confined spaces or sensitive environments without the extensive infrastructure and high capacity of larger dredgers.
It’s important to assess the project’s duration and frequency. Long-term projects with continuous work might benefit from investing in more robust and enduring equipment. In contrast, temporary or occasional projects could find rental options or modular dredging equipment more cost-effective.
Also, consider the logistical aspects of the project site. Remote or inaccessible areas might limit the size and type of dredging equipment that can be employed, favoring portable and easily transportable dredging systems.
Lastly, planning for the scale should integrate with the anticipated volume and type of material to be dredged, as this will impact machinery choice and overall project efficiency.
Dredging Support Equipment
Tugboats are critical in maneuvering larger dredgers into position and are essential for towing split hopper barges to disposal sites. Work boats serve multiple support roles, such as crew transfer and overseeing dredging operations to ensure safety and efficiency.
Split hopper barges are integral for transporting dredged material, especially when the disposal site is distant from the dredging location. They split into two, allowing for rapid unloading of materials at the designated disposal areas.
These auxiliary vessels and equipment help optimize the dredging process, making operations smoother, safer, and more efficient. Their roles might be supportive, yet their impact on the success of a dredging project is substantial.
Tugboats
Playing a vital role in dredging operations, these robust vessels facilitate the positioning and movement of dredgers and barges. Given their potency, they can maneuver the equipment even in confined spaces, ensuring precision and safety.
With their strong pulling power, they are especially critical when transporting dredged material or when dredge systems must be relocated in response to shifting conditions or project phases. Furthermore, tugboats contribute to operational efficiency by assisting with the assembly and disassembly of modular dredging equipment, showcasing their versatility within the dredging process.
Whether facing turbulent waters or tight deadlines, these mighty helpers are indispensable for keeping projects on course.
Work Boats
Critical to the success of dredging operations, work boats serve multiple roles. These versatile vessels are known for their ability to transport crew and equipment swiftly to various locations on site. Typically smaller and more maneuverable than other dredge support equipment, they are essential for a range of tasks including positioning anchors for dredgers, towing small barges, and surveying the dredge area to ensure accuracy and efficiency.
Additionally, work boats often come equipped with cranes or winches to assist with lifting operations and can provide emergency support if needed. Their adaptability makes them a vital component in maintaining the smooth operation of the dredging process, enabling quick response to changing conditions or unforeseen situations. In essence, work boats are the multitasking powerhouses of dredge projects, keeping all elements connected and operational.
Split Hopper Barges
Split hopper barges are an integral part of dredging operations, serving as the primary means for transporting dredged material to disposal sites. Their bottom-hinged halves can be swung open to release the load rapidly, a design feature that dramatically enhances the efficiency of depositing the dredged silt, sand, or other materials.
Often propelled by their own engines or towed by tugboats, these barges are especially useful in open water where the material can be disposed of at sea, subject to environmental regulations. Their sizes vary, accommodating different volumes of dredged material, which enables them to be used in a range of project scales, from small coastal works to large-scale land reclamation.
Their versatility extends to their ability to navigate both coastal environments and inland waterways, proving them to be a valuable asset in various dredging projects.
Hydraulic Dredging Vs Mechanical Dredging
Hydraulic dredging employs water to excavate and transport sediment via a pipeline, thereby creating a slurry mixture that is easily pumped. This method is effective for projects that require the movement of fine sediments over long distances. High precision and minimal disruption to the dredged material make it suitable for environmentally sensitive areas.
Mechanical dredging, on the other hand, uses heavy equipment such as buckets, grabs, or backhoes to physically scoop and remove sediment. The collected material is then transported for disposal or use elsewhere. This technique allows for the easy removal of bulky debris or coarse materials. It is typically faster in terms of excavation but can be less precise than hydraulic methods.
In choosing between the two, project specifics such as sediment type, disposal location, environmental considerations, and budget constraints are critical factors. Hydraulic dredging often requires a higher initial investment but can be more cost-effective over time, especially where sediment relocation is concerned. Mechanical dredging offers quick mobilization and high productivity, making it ideal for shorter-term or smaller-scale operations.
Advantages of Hydraulic Dredging
Hydraulic dredging stands out for its precision and minimal environmental disruption. Employing a cutterhead or suction mechanism, it effectively liquefies soil, allowing for the smooth pumping of sediments through pipelines.
This method is particularly efficient for large-scale projects owing to its continuous operation, which translates to higher productivity over time. The capacity to pump material over long distances makes it versatile for projects like land reclamation and harbor deepening, where the disposal area might be far from the dredging site.
Additionally, the reduced turbidity compared to mechanical methods helps to preserve the aquatic ecosystem, making it a more sustainable choice in sensitive environments.
Advantages of Mechanical Dredging
Mechanical dredging boasts precision in excavation, easily tackling defined areas without disturbing adjacent sites. Its robust equipment and straightforward operation make it ideal for projects requiring the removal of hard-packed or rocky seabeds.
Quick mobilization and demobilization enhance its suitability for short-term endeavors with tight deadlines. Furthermore, the dredged material, once extracted, is easy to transport for immediate use or disposal due to its relatively dry nature, reducing the environmental impact of spillage en route.
This method can be a cost-effective solution, minimizing the need for extensive support vessels and ancillary equipment. The clear-cut nature of mechanical dredging operations allows for a more controlled approach to managing environmental interactions, especially when dealing with contaminants that require careful containment.
Cost-Efficiency in Dredging Operations
Minimizing costs without compromising efficiency is a significant consideration in dredging operations. The initial investment costs for dredge equipment can vary widely. Larger, more complex machinery like cutter suction dredgers demands higher upfront capital compared to simpler, smaller equipment such as a plain suction dredgers.
Operation and maintenance costs also play a crucial role in the overall cost-efficiency of a dredging project. Fuel consumption, crew requirements, and wear and tear on machinery parts greatly influence these ongoing expenses. Hydraulic dredgers, while often more efficient in terms of productivity, may exhibit higher fuel costs relative to mechanical dredgers, which might have lower fuel requirements but possibly slower operation rates.
To enhance cost efficiency, project managers need to match the type of dredger with the project’s scale and specific conditions. Selecting a dredger with capabilities beyond the project’s demands can lead to unnecessary expenditures, while choosing a dredger that’s too small or not powerful enough can lead to delays and increased costs over time.
Additionally, the resale value of equipment should be taken into account. Some types of dredgers, particularly those with wide-ranging applications and high demand, can retain value better and offer a more substantial return on investment upon resale.
Moreover, investing in regular maintenance schedules helps to mitigate the risk of costly equipment failures and downtime. A well-maintained dredge can operate more efficiently, reducing the risk of unexpected budget inflations due to emergency repairs or equipment replacement.
Initial Investment Costs
Investing in dredge equipment often represents a substantial financial commitment. The costs vary depending on the type, size, and capability of the dredger. Mechanical dredgers like bucket ladder and grab types are generally less expensive up front compared to large hydraulic dredgers, such as cutter suction dredgers which require more intricate engineering and construction.
For small to medium-scale projects, smaller dredgers or even pre-owned equipment may be cost-effective solutions. However, large-scale endeavors might necessitate high-capacity, new hydraulic dredgers which, despite their higher initial price tag, can deliver long-term value through efficient operation and reduced labor costs.
Essential to consider are the technological features and automation level of the equipment. Advanced automation may entail higher initial costs, but it can lead to better precision, resulting in lower operational costs over time.
Prospective buyers must evaluate not just the purchase price but also the projected lifespan of the equipment and potential resale value. Robust build quality and reliable brand names often maintain their worth better, easing the financial burden over the entire period of ownership.
FAQ
What type of equipment is used in dredging?
The type of equipment used in dredging mainly includes mechanical or hydraulic dredgers like trailing suction hopper dredgers.
What tool is used to dredge?
The most common tool used for dredging is the plain-suction dredge.
What are the classification of dredgers?
Dredgers are classified into trailing suction hopper dredgers, cutter suction dredgers, dry dredgers, dipper dredgers, water injection dredgers, and stone dumping vessels.
What is the operational process of a cutter suction dredger?
A cutter suction dredger operates by cutting and sucking up seabed materials then discharging them through a pipeline, often used in harbor deepening and maritime infrastructure projects.
How does the environmental impact of dredging vary with different equipment?
The environmental impact of dredging varies greatly with different equipment as some, like mechanical dredgers, can cause more severe seabed disruptions and sediment dispersal, whereas others, like suction dredgers, offer a degree of precision and less environmental disturbances.
What roles do mechanical dredgers play in harbor deepening projects?
Mechanical dredgers play an essential role in harbor deepening projects by removing accumulated sediments, ensuring safe and efficient navigation, and preventing potential hazards for incoming vessels.
Recap: